Minimizing cost and time overruns with construction project management software
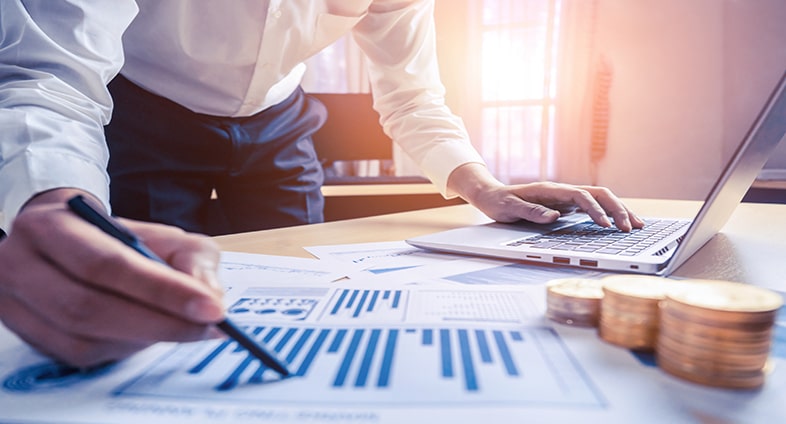
In 2021, as businesses continue to digitize operations with a vengeance, the question arises: what sort of opportunity does this ‘enforced digitization’ offer to companies struggling with cost and time overruns in project management?
Daniel, our CEO, and project management expert Abrachan Pudussery breaks down 4 key steps that can prevent almost any type of time or cost overrun in an infrastructure or construction project. But there’s a catch: those steps are possible only with modern (read, 2018-and beyond) software technology, specifically ‘cloud’ project management software for construction. Fortunately, such software has been readily available since the latter half of the previous decade, although it was only post the pandemic that ‘digitization’ and ‘automation’ and ‘integration’ started becoming common parlance in the EPC sector.
“Technology platforms can be implemented to provide project managers with the accurate project progress information they need to be able to forecast schedule and cost variances, early enough to allow them to avoid serious problems. Automation of project workflows, with pre-defined rules of credit for key workflow stages, provides an accurate basis for management of earned value, without requiring input from individual team members, and avoiding different interpretations of how much work has been completed. In making the shift to WFH, many companies have now successfully set up a digital collaboration platform, with video conferencing, and design-interfacing tools. They now have a way to allow employees to share data, interact, discuss, meet deadlines, and keep work going without too much disruption. By utilizing cloud work platforms, existing processes have been translated into the virtual space. Initially, work will be accomplished using the established process – but without the safety net of dedicated human overseers and careful manual management. Not only will previous inefficiencies exist, they’ll most likely amplified. That’s why companies need to set up new ways to manage resources working remotely, and to enforce protocol across teams, more aggressively than before. “ Taken from the whitepaper “Post-pandemic workforce transformation potential in the engineering consulting industry”. Download it here. |
Broadly, the 4 steps towards minimizing time/cost overrun in construction projects are:
Step 1: Define a set of schedule and budgetary monitoring parameters that will help managers accurately assess progress. This means detailing down project milestones to the lowest level at which the cost and schedule can be reliably estimated, which means a more aggressive approach to planning where the schedules of the project’s contractors and sub-contractors plug into the project management system so that managers can see the exact impact a delay in one specific problematic milestone could have on the overall project.
Step 2: Devise ways to accurately measure the progress of an activity. For all practical purposes, ‘progress’ in a modern project is measured by how well (or not) a deliverable adheres to the QMS, the budget, and the schedule. This kind of scheduled-based monitoring is a good start but not really enough anymore; today’s savvy project manager needs a little extra help in defining, tracking, and enforcing that adherence. And that is where techniques like EVM or Earned Value Management comes in. EVM is not new but until recently fell into the ‘good but impractical’ category of project management techniques. Today, with EVM-friendly software, managers can easily add in the necessary components of EVM to track if work is progressing according to the plan, and if not, to take corrective actions to catch up and complete the work as stipulated.
Step 3: Digitally link schedules with costs. Today, the digital Work Breakdown Structure (WBS) is stored in scheduling software like Primavera, and the digital Cost Breakdown Structure (CBS) is stored in the ERP like SAP, and neither really ‘talks’ to the other; each is updated and monitored manually. So, when a delay occurs, as it often does, managers have no way to figure out the impact that delay will have on the project’s costs and bottom line, except manually – which is neither foolproof nor efficient. That is why linking Schedules to Costs from within the system is so vital, if companies are to have any real hope of de-risking their cashflows.
Step 4: Aim for ‘holistic’ risk management. Even pre-pandemic, companies had to tightly monitor risk, safety, quality and their resources to keep business running at all, in a industry where one small defect or failure in the build can snowball into huge losses (re-construction, delayed facility operations etc.). Post-pandemic, this need will only intensify, because as businesses continue to digitise across operations and become ‘holistic’, not only will everything become increasingly transparent, any delay or overrun or error that is potentially damaging to a project’s successful completion can now be nipped in the bud, in theory at least.
Step 0: Connect everything. People, process, data.
If I’m being nit-picky, the above are actually sub-steps. The first fundamental step is to integrate project data and then by the subsequent ripple effect, the people and the processes that utilize that data will integrate naturally. This Step 0, if you will, is actually good news for the EPC industry, given the way project companies typically work, where many EPC organizations still have their data in multiple isolated systems. That is why I believe that setting up a single common platform and integrating all the siloed data into a common pool of data shared smoothly across all the systems becomes the first and most basic step in even the simplest kind of ‘digital transformation’ initiative. Up until COVID, I suspect that the scale of that connecting and integrating seemed intimidating to most engineering companies, especially the large multi-located ones, but now with the surprisingly smooth transitions they had to undergo in response to the pandemic restrictions, companies are beginning to realize that if senior management concurs on the need for such a ‘transformation’, the actual implementation of that transformation is actually simpler than it sounds. Once the digital system has been installed and configured, the organization just needs to roll it out, tweak it, and train personnel to use it.
To conclude, technology can be more than a means of communication. It can drive growth and enable the proactive rather than reactive methods of project management that are far more likely to help control costs in a modern project. Technology can enable a holistic approach that will create transparency with respect to schedules, link cost and scope and schedules, and implement best practices like EVM and Agile which will in turn create the necessary efficiency in time and budget management.
(Some of these topics have been discussed at length in a podcast with Daniel, Sanjay, and Abrachan. (Watch Podcast) To further discuss any of the topics mentioned in this blogpost, or in the podcast, contact me on my mail where I’ll also be delighted to answer any questions. Alternatively, you could subscribe to our new ‘Work as One’ podcast series where my colleagues talk about how technology in engineering and construction.)
Signoff.